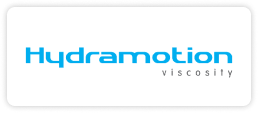
Produkter
Hydramotion – Viskositetsmåling
Hastighed, holdbarhed og utrolig følsomhed er kendetegnene ved de unikke viskositetsmålere ReactaVisc og goVisc. Uanset om det er en reaktionsbeholder eller et reagensglas, er disse de perfekte værktøjer til præcisionsviskositet i alle indstillinger, lige fra forskning til produktion.
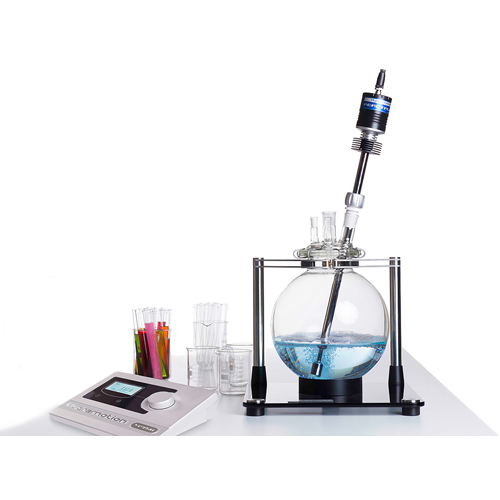
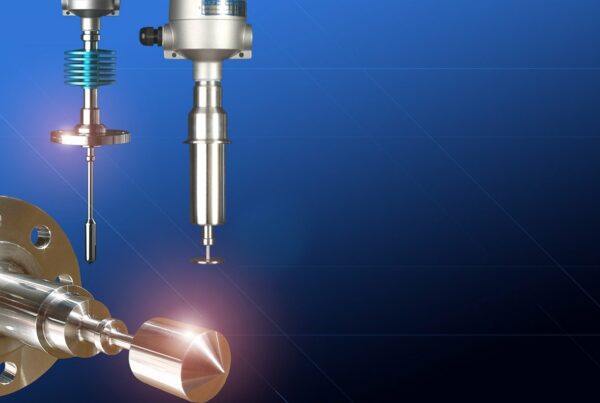
Den perfekte løsning
Et meget let og bærbart instrument med den velkendte Hydramotion-præcision og pålidelighed. Viscolite fungerer i enhver væskevolumen – bare dyp og aflæs. Den er også utrolig robust, så du kan endda røre væsken med den, mens du måler viskositeten!
Med sin lange batterilevetid og bæretaske er den den perfekte løsning til viskositetsmåling på farten, enten ude i marken, på fabrikken eller i laboratoriet.