Hycontrol is the market leader with sensors and systems for controlling foam. The foam sensors are exclusively designed to detect foam in water-based and non-water-based liquids.
Applications
Foam is a major problem in many biotechnological and other industrial processes.
Typical areas of application are the production of food and beverages, printing ink and paint, water and
waste water treatment and biogas production, where the sensors are in reactors, evaporators, plants
for vacuum cooling and aerobic as well as anaerobic fermenters. Is there a very special foam problem in one
industry, Charis is able to develop both hardware and software to solve the problem.
Benefits of better foam control
– Increased throughput in production by reducing downtime
– Reduced product loss
– Addition of antifoam is optimized and costs are reduced
– Reduced spillage and contamination due to foam overflow
Foam control – explained
Six powerpoint slides to demonstrate the basic method of foam control with the Hycontrol foam control system.
Foam control systems – product range
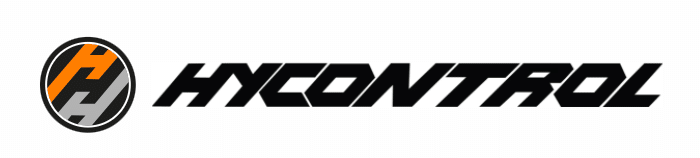
IMA Sensing® technology – provides immunity to soiling of the sensor
With the patented Multi Action sensing technology “IMA Sensing® technology”, Hycontrol sensors are able to distinguish between the remaining coatings of foam and product that build up on the sensor itself, and the foam that occurs during the process. Due to this unique technology, the sensors have great accuracy and high reliability.
The foam sensor ignores the inevitable soiling while continuing to monitor the foam. No matter how much the sensor is coated, or how dense and sticky the coating is, the unique construction makes it possible to measure the foam during the entire process
The picture on the right shows a Hycontrol sensor coated with a sticky mass of foam and product. The measurement current, shown in red, continues to flow only through the foam. The blue line represents the leakage current driven by the protective electrode. This enables the sensor to function as the leakage current is measured separately and not as part of the foam signal.
It is often not possible to prevent the build-up of coatings, but “IMA Sensing® technology” enables the sensor to function reliably despite extensive coating or soiling. You can see a short video demonstration of how “IMA Sensing® technology” works, please click here
The photographs on the left show a Braun fermenter coated with product. In the enlarged image, the red arrow points to the sensor. It can be seen that it is completely covered with material, but it was still fully functional when the container was opened. The user was so amazed that he took a photograph and sent it to Hycontrol.
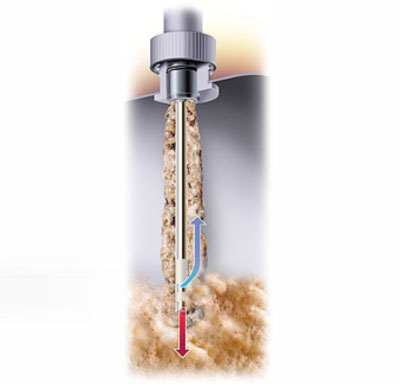
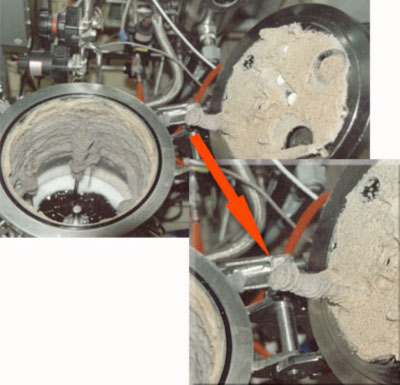